Top Breakdowns by VMRS Code: What They Reveal and How Fleets Can Respond Smarter
VMRS codes exist to standardize the way fleets and repair shops record maintenance issues. But with over 28 thousand possible codes, it's not easy keeping up. We walk you through what they are and the most common issues we see in the fleets we manage.
7/2/20256 min read
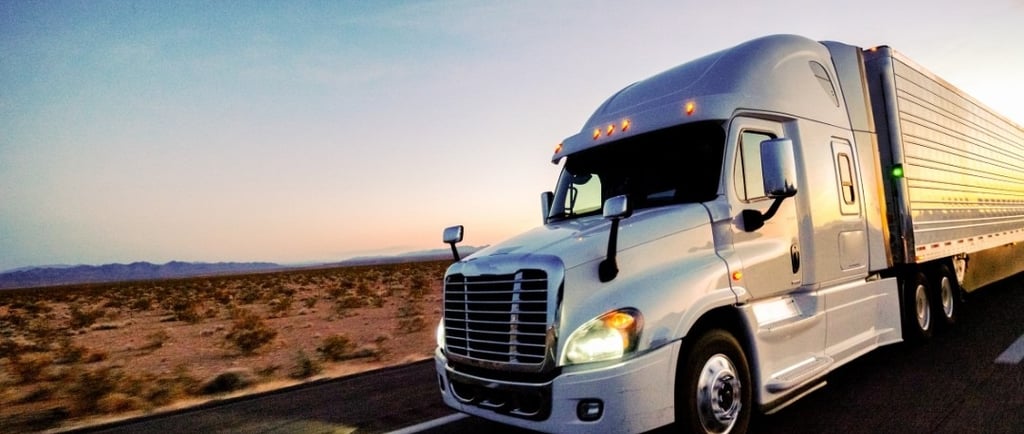
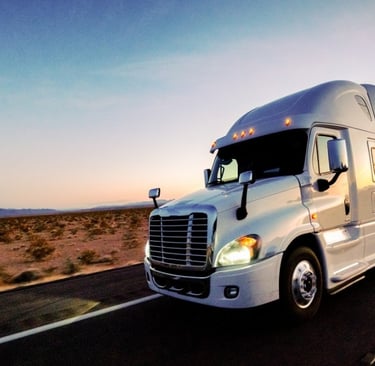
When it comes to managing a fleet, data is one of your most powerful tools. And one of the most insightful data sets in the industry comes from the Vehicle Maintenance Reporting Standards (VMRS) codes developed by the Technology & Maintenance Council (TMC) of the American Trucking Associations. These codes categorize and track every aspect of truck maintenance, enabling fleet managers to pinpoint the most common breakdowns, plan preventative maintenance, and reduce costly downtime.
What is VMRS and Why Does It Matter?
VMRS stands for Vehicle Maintenance Reporting Standards, a universal coding system that allows fleets, technicians, and service providers to speak the same language when it comes to maintenance and repairs.
Originally introduced in 1970 by the American Trucking Associations' Maintenance Committee, VMRS was designed to eliminate the confusion and inconsistency in how breakdowns, repairs, and labor were being recorded and reported across the industry.
This standardized system was created out of necessity. At the time, each fleet or shop had its own methods for tracking maintenance, which made it nearly impossible to benchmark performance or identify trends across vehicles and locations. The ATA launched VMRS to solve this problem by creating a consistent, comprehensive code structure that anyone in the industry could adopt.
The coding system itself uses a structure with nine-digit codes divided into three segments:
System (first three digits): Identifies the broad system of the vehicle, such as brakes or tires.
Assembly (middle three digits): Specifies the particular area within that system.
Component (last three digits): Indicates the exact part or failure being addressed.
In addition to the primary codes, VMRS includes over 60 supporting “code keys” that identify things like labor hours, technician activities, failure reasons, and even warranty status. This depth allows for granular insights into cost, performance, and recurring issues.
VMRS has evolved significantly over time, especially with the growth of electronic diagnostics and telematics. It’s now integrated into many leading fleet management systems and maintenance software platforms, making it easier than ever to collect and analyze data in real-time.
Clearly, VMRS codes are complicated. A language of their own. We don’t expect you to memorize each and every one of them, so we’ve included
According to our own aggregated data and field reports, three categories consistently top the list of VMRS-coded breakdowns: tires, air leaks, and towing incidents. Below, we break down each category, explore what the data means, and offer proactive strategies your fleet can implement today.
Tire-Related Breakdowns
Tire issues are, without question, the leading cause of roadside breakdowns. According to our internal breakdown data, tire issues make up over half of all reported service calls. But not all tire breakdowns are the same:
Worn-Out Tires: 50% of Tire Breakdowns
Worn-out tires aren’t necessarily a bad thing. In fact, they can be a sign that your tire lifecycle is being fully utilized. A worn tire that needs replacement at the right time is far less costly than a premature blowout. Preventative replacement costs around $300-$600, depending on the tire type and brand. Whereas a blowout is significantly more expensive. The FMCSA estimates blowouts cost, at minimum, an average of $2,000, not even facturing in collateral damage, towing, and downtime.
Bulk tire replacements in-shop are more cost-effective, saving on labor hours and enabling better negotiations with tire vendors. Companies like ours specializes in negotiating better prices for bulk tire replacements and labor, adding a layer of strategic value to your maintenance plan.
Tire Blowouts: 20% of Tire Breakdowns
Tire blowouts are often preventable and are typically the result of low tire pressure gone unchecked. A flat tire driven on too long damages the tire structure, leading to catastrophic failure. Blowouts can cause collateral damage to:
Brake lines
Rims
ABS systems
Adjacent tires
The best prevention strategy is emphasizing thorough pre- and post-trip inspections. Training drivers to recognize low tire pressure and respond promptly is a must. In many cases, blowouts are a symptom of missed inspections rather than random chance.
Tire Damage: 15% of Tire Breakdowns
Tire damage from road hazards such as nails or curb strikes can be unavoidable, but it should be tracked closely. According to our internal data on breakdowns, these kinds of incidents account for up to 15–20% of all tire failures in commercial fleets.
While these are oftentimes unavoidable, they’re not untrackable. It's crucial for fleets to track where these tire-damaging events occur. If your drivers or technicians are reporting frequent flats in a specific location — like your yard, a distribution center, or even a customer site — it’s time to investigate. Repeated damage in a tight geographical footprint often points to environmental hazards: construction debris, broken pallets, stray fasteners, or poor infrastructure maintenance.
Miscellaneous Tire Issues: 15%
The remaining percentage is a mix of sidewall bulges, valve stem failures, and unbalanced wear patterns. These are indicators that routine maintenance schedules or alignment processes may need revision.
Air System Leaks
Air leaks may seem minor at first, but they can quickly escalate into safety issues or even roadside shutdowns. These can lead to loss of brake pressure, potentially causing the brakes to lock up or fail, and may result in accidents. Here are the most common culprits:
Service Line Leaks
Service lines are vital for air brake operation. A minor leak, if caught early, is inexpensive and easy to repair. However, if ignored, it can lead to Out-Of-Service (OOS) violations or complete brake failure. These types of leaks are often discovered during pre-trip inspections. When missed, they escalate quickly into road calls.
To check for service line leaks during a pre-trip inspection, build full air pressure, release the brakes, and hold the service brake pedal while monitoring for excessive pressure loss (more than 4 PSI in one minute for combination vehicles). Walk around and listen near the blue service line gladhand for hissing, or use a soap solution to detect bubbles around fittings. Any signs of leaking indicate a faulty hose, loose connection, or bad seal that must be repaired before driving.
Underbelly Air Line Leaks
These are often identifiable by a constant hissing sound and are easily overlooked unless drivers are trained to recognize them. Underbelly leaks can lead to:
Low tire inflation (if connected to air inflation systems)
Brake system failure
Chain-reaction breakdowns due to misdiagnosis
Driver education is again a key solution here. Drivers should be encouraged to report any unusual hissing sounds or performance issues immediately. To check for underbelly air line leaks, release the brakes and listen closely along the underside of the trailer while air is pressurized, especially around elbows, crossmembers, and suspension components where lines are routed. Use a soap and water solution if needed to spot bubbles at fittings or worn areas. Any audible hissing or visible damage should be addressed immediately before the trailer is moved.
Compressor Leaks
Newer trucks, especially Peterbilt models, sometimes suffer from clogged air purge valves. This can result in air compressor leaks, but a simple cleaning around the valve is often enough to fix it. In more serious cases, compressor failure might point to deeper problems in the air system, such as humidity accumulation due to a faulty air dryer. These types of leaks should always trigger an inspection of the full air system to identify root causes.
Towing Events
Towing is one of the most expensive breakdown outcomes and should be avoided whenever possible. Our data tells us that towing typically falls into three categories:
Towing Due to Electrical Breakdown
The majority of towing calls are caused by aftertreatment or electrical system failures. Today’s diesel engines are equipped with complex systems like Diesel Particulate Filters (DPFs) and Selective Catalytic Reduction (SCR) systems. When these systems malfunction, trucks will enter a staged derate process:
Check Engine Light
Speed restricted to 55 mph
Speed restricted to 30 mph
5 mph derate or complete shutdown
Drivers who fail to report a Check Engine Light promptly risk escalating the issue to the shutdown phase. Fleet managers must make sure drivers are trained to understand and act on each stage of this process. Catching the issue early allows the truck to be rerouted to a nearby repair shop, avoiding the need for a tow.
Towing Due to Mechanical Breakdown
Mechanical issues such as failed drivetrains, broken axles, or seized transmissions may also require towing. These types of failures are less common but can be far more expensive. A cost-benefit analysis should always be done to determine whether on-site repair or towing to a shop is more economical. Partnering with a provider like MFA, which has a nationwide network of vendors, can make this decision easier and more cost-effective.
Towing Due to Impound
While not technically a mechanical breakdown, impounds still result in expensive tows and fines. Impounds may occur due to illegal parking, expired registration, or other violations. To mitigate this risk:
Train drivers on local regulations
Encourage photo documentation of parking areas
Contact local law enforcement if a tow feels predatory or unjustified
Predatory towing is a growing concern, and knowing your rights in each municipality can help protect your fleet.
Turning VMRS Codes into Fleet Strategy
Breakdowns are inevitable in any fleet operation, but how you respond to them can be the difference between profit and loss. VMRS codes provide a transparent and standardized way to identify the most common breakdowns and their causes. By paying close attention to high-frequency codes like those related to tires (017), air systems (013), and towing (034), fleet managers can:
Improve driver training
Optimize maintenance schedules
Reduce unexpected costs
Increase uptime and profitability
Partnering with a solution like My Fleet Assist adds an extra layer of support, helping you:
Negotiate better labor and parts pricing
Improve breakdown response
Minimize downtime
In short, the top VMRS breakdowns reveal more than what’s going wrong—they highlight where fleets can grow stronger, more efficient, and ultimately more profitable.
Get in Touch!
Tired of trying to decode VMRS codes? Partner with us and we'll handle your breakdowns for you.
Location
465 Crossroads Pkwy., Bolingbrook, IL, 60440
Working Hours
Mon-Sun 24/7
Contacts
(630) 389-4469
business@myfleetassist.com